Not since the 19th century, with the arrival of the first motor vehicles, including electric, have...
Necessities for Coiling and Reeling Extruded Tubing
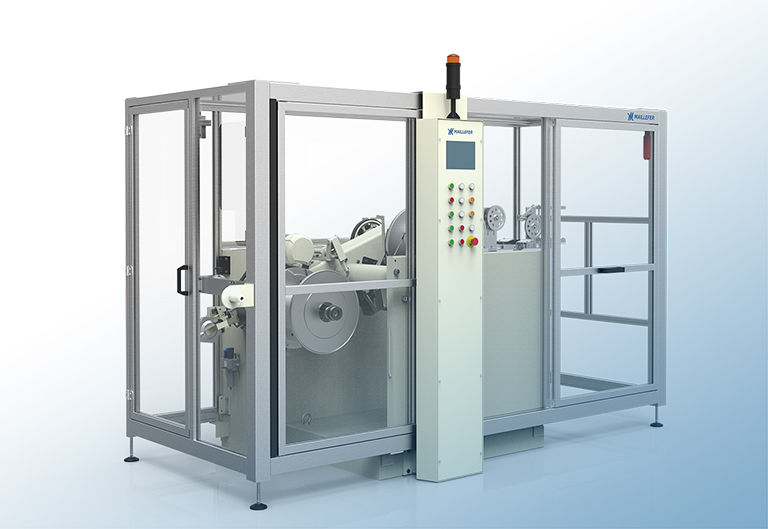
Selecting the right coiling and reeling technology for your extrusion tubing application is essential. Keeping the tubing together while maintaining tube integrity during transport is what it’s all about! It’s also imperative to ensure operator safety during unloading. We’ve put together a few tips based on Maillefer technology to ensure the best possible outcome for coiling and reeling extruded tubing.
Use the latest drive and control technology.
- The winding pitch should be automatically calculated using pre-programmed tube sizes while allowing fine-tuning during production.
- The dancer should have modern sensing technology for an extra-light touch on the tube. This is especially important for medical tubing where we recommend a contactless dancer to ensure product quality.
- The end limits for reversing winding direction should be given by adjustable sensors, allowing for full edge-to-edge lays. This includes defining how a full reel is completed, either at its exact length or just a bit more to finish the lay-up to the edge.
Always ensure operator safety.
- Dual coiling, safe fully-automated transfers, and ergonomic handling all play a role in operator safety, and in ensuring the quality of finished coils or reels.
- Cut-off, strapping and coil unloading should be done automatically and safely within an operator-free enclosure.
- Reels that unload from the front side should be at a convenient height for the operator. The unloading door should be positioned to protect the operator from the winding side of the machine when opened.
- Reels that unload from the backside should be at a convenient height for the operator. Use a reel-lift for large reels. As with front side machines, the unloading door should be positioned to protect the operator from the winding side of the machine when opened.
Consider the application.
- Automotive, heating and plumbing, irrigation, micro-duct and special tubing are typically wound on strapped coils. Tubing should be run at a constant speed without interruption or ramping during coil transfers. Optional automatic coil ejection onto a trolley or reception table is recommended.
- Medical tubing is typically wound onto a stainless steel fixed bobbin. The line speed in relation to rotational speed should be synchronized with traversing and switchback capabilities in order to achieve perfect lays. The goal is to have a smooth and clean finished coil, without gaps, overlaps and tube compression (ovality).
- For irrigation tubing, automatic reelers are typically used to wind flat irrigation laterals onto cardboard reels. Consistent speed without interruption or ramping during coil transfers is important.
Maillefer supplies several coiling and reeling machines based on application, tube diameter range, maximum coil diameter and linear speed. These options can be viewed at https://www.maillefer.net/en/components/coilers-and-reelers/.
Have a question about this blog or want to inquire about a product? Comment below or email marketing.